EB drilling proves much more economical when processing work pieces requiring a large number of drilled holes on each component. Some typical examples where electron beam perforation is applied are drilling extrusion plates for glass fibre production, or manufacturing all types of filter plates. Work pieces are put into the drilling position by 4 or 5 axis manipulators or by rotational and linear movement mechanisms, which accept plates rolled into cylinders.
The benefits of electron beam drilling
- Extremely high drilling frequency (up to 3000 boreholes per second) compared with other drilling methods due to „on the fly drilling”
- Narrow drill diameter and position tolerances
- Work pieces of any hardness and surface composition processed without wear
- Electron beam parameters can be quickly changed in cases of complex drilling geometry
- Angular hole axes with flat angles to the surface
Details
- Work chambers from 0.8 to 2.5 m³ and above
- Extremely high drilling frequency due to “on the fly drilling” with simultaneously moved beam
- Precise drill diameter and position tolerances, burr-free boreholes on the beam emission side
- Work pieces of any hardness and surface composition processed without wear
- Beam parameters can be quickly changed in cases of complex drilling geometry
- Easily programmable CNC control system
- Angular hole axes with flat angles to the surface
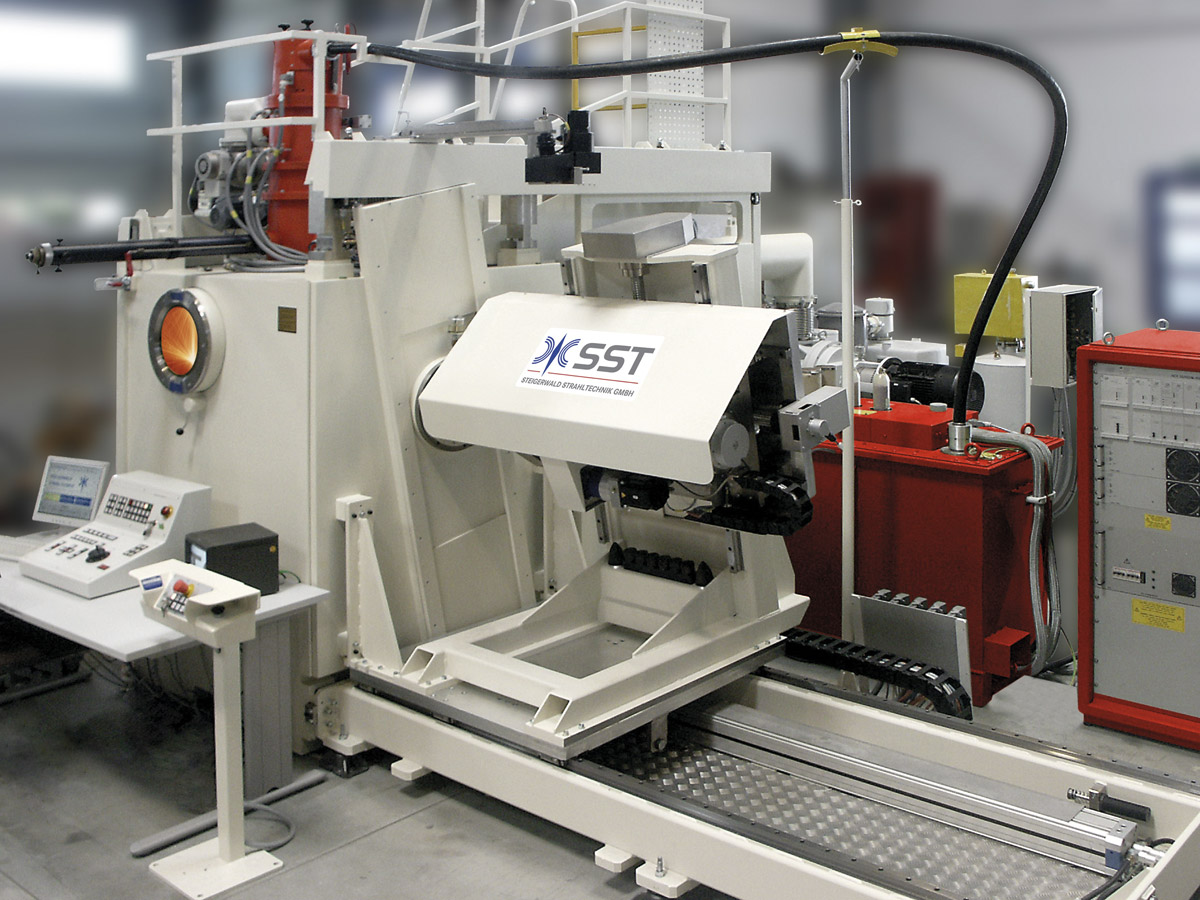